What Is Design for Manufacturing?
Design for Manufacturing (DFM) is the practice of engineering your product in a way that makes it easy, efficient, and cost-effective to build — without compromising its function, form, or future.
At BrahmWorks, we embed DFM into every stage — from initial sketches to production-ready files. We don’t treat it as a checkbox after design is done — it’s a continuous, iterative dialogue between design, engineering, and fabrication.
This matters even more when scaling hardware: A design that looks great in CAD can cause production nightmares if real-world constraints aren’t considered early on — tight tolerances, awkward geometries, or overlooked assembly flows can balloon your costs and timelines.
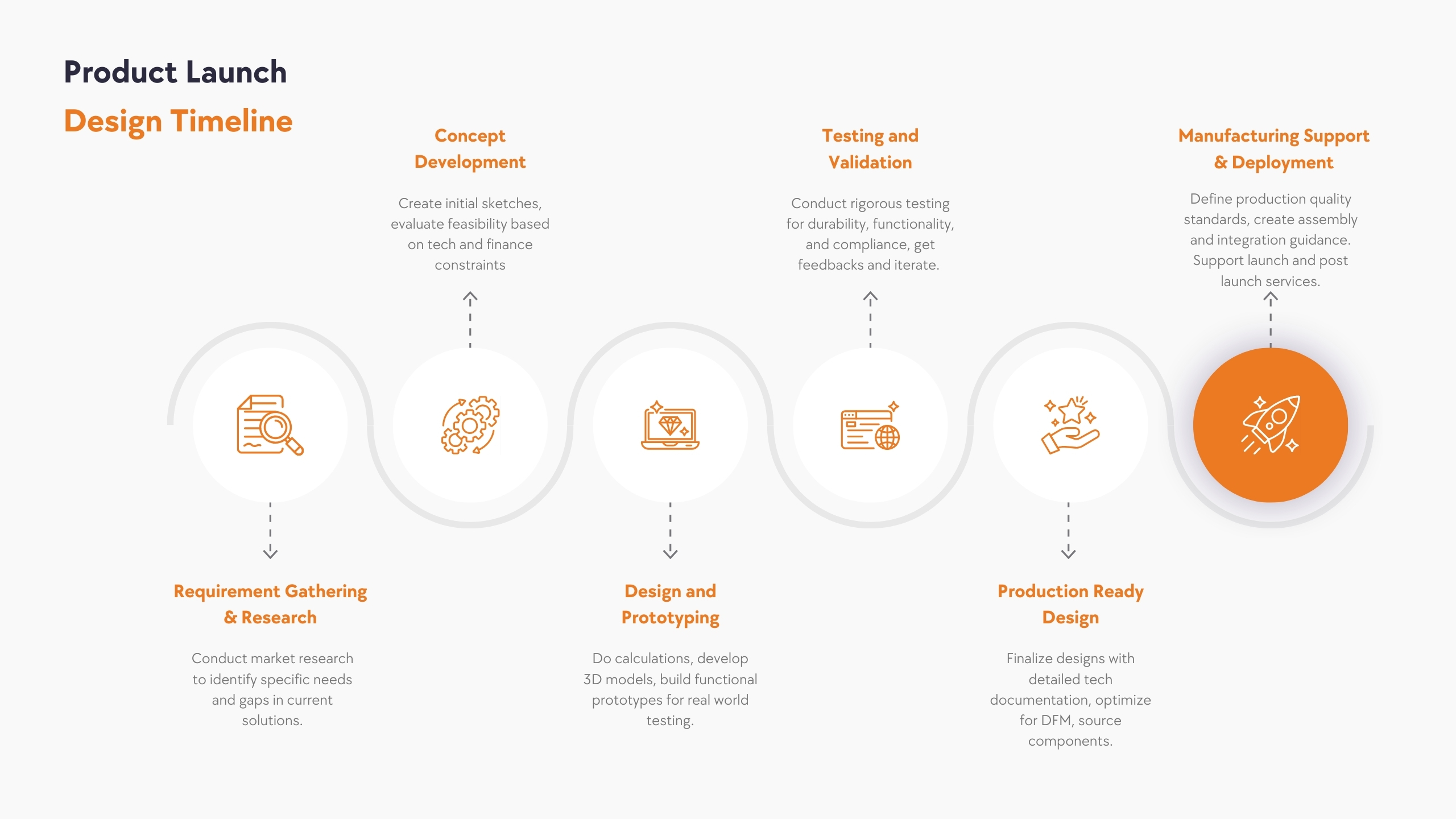
stages of product design development
Why DFM Matters
Here’s what we’ve experienced firsthand when DFM is done right:
- Lower Production Costs: Reduce part complexity, material waste, and assembly time.
- Faster Time to Market: Spot manufacturing blockers before tooling or prototyping.
- Consistent Quality: Prevent variability and reduce QA rejects with design choices.
- Ease of Scaling: Adapt easily between small batch and high-volume production.
- Reliability: Fewer parts and simpler mechanisms lead to more robust products.
- Supplier Collaboration: DFM encourages clearer communication and faster iterations.
- Sustainability: Less waste. Smarter materials. Greener systems.
The BrahmWorks DFM Principles
These principles are baked into every design we build — whether it’s a robotics platform, smart device, or a full-stack embedded product.
1. Minimize Part Count
Fewer parts = fewer headaches. Reducing part count simplifies procurement, assembly, and maintenance — and leaves less room for failure.
We often ask: Can we combine these into one molded part? Can this be folded from a single metal sheet? If yes, we redesign.
But we don’t compromise function for minimalism. There’s always a tradeoff between multifunction parts and ease of manufacturing — and we tune the balance depending on volumes, tolerances, and cost targets.
2. Use Standard Parts Wherever Possible
Reinventing the wheel is expensive. Where applicable, we design around off-the-shelf components — screws, brackets, bearings, displays, connectors, and more — to speed up builds and reduce sourcing risks.
This also means less time fighting supply chain issues, and more time building working systems.
3. Design Modularly
Our designs are like building blocks — modular, testable, and swappable.
Modular thinking lets us parallelize work streams (electrical, mechanical, firmware), accelerate prototyping, and future-proof upgrades. It also makes serviceability and repairs easier — a crucial factor in hardware maintenance post-deployment.
4. Make It Easy to Fabricate
We tailor designs based on how they’ll be made. That means:
- Draft angles for injection-molded parts
- Bend radii for sheet metal
- Tapped holes and thread inserts for CNC machining
- Avoiding undercuts or overhangs unless justified
Before finalizing a design, we ask ourselves: Can a factory build this repeatedly without errors?
5. Optimize for Assembly
Even the most elegant part becomes a bottleneck if it’s hard to assemble. We optimize designs for intuitive, tool-less (or minimal-tool) assembly wherever we can. That includes:
- Top-down assembly orientation
- Self-locating tabs and features
- Snap fits and integrated fasteners
- Symmetrical parts to avoid misalignment
DFM overlaps with DFA (Design for Assembly) in this space, and we treat them as two sides of the same coin.
6. Be Smart with Tolerances
Tight tolerances = high costs. We use tight fits only where needed (e.g., sealing interfaces, optical alignments), and leave room elsewhere.
Our team performs worst-case tolerance analysis — especially for parts with mating surfaces across different materials (plastic on metal, PCB inside an enclosure, etc.).
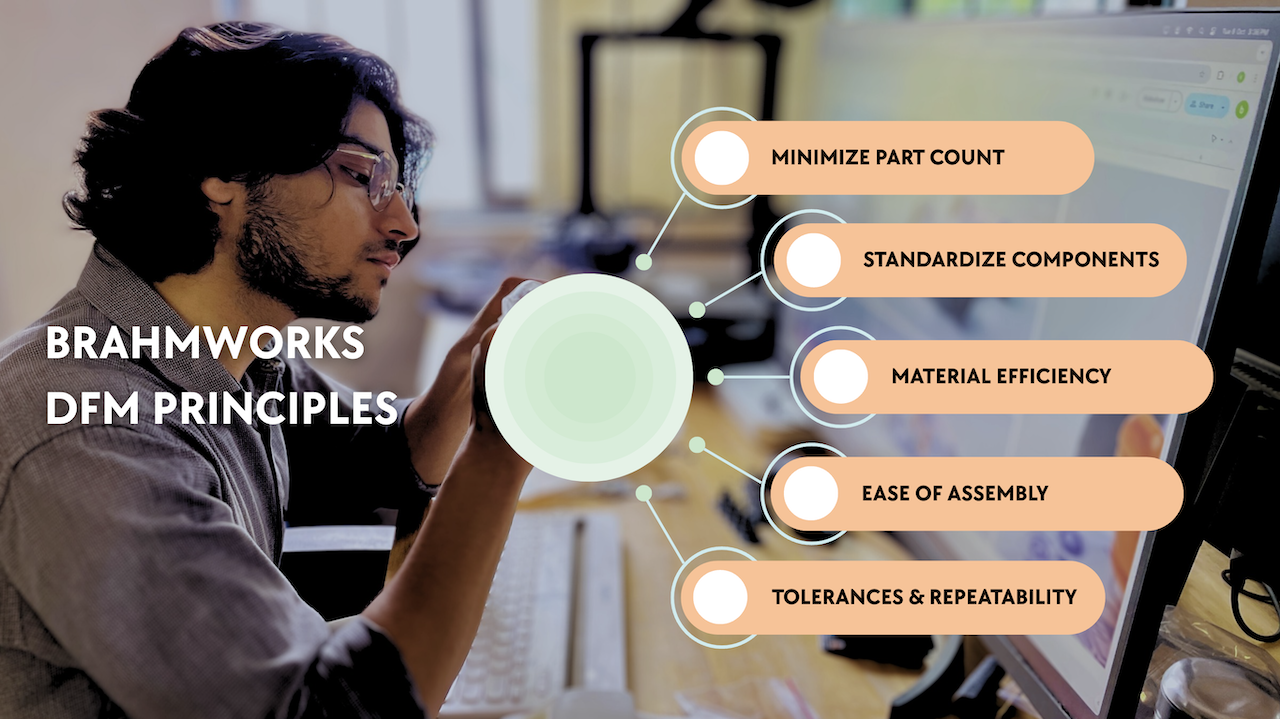
BrahmWork DFM Principles
Best Practices From the BrahmWorks Workshop
🔧 Involve the Fabricators Early
We don’t just throw designs over the wall. We talk to fabricators, vendors, and assemblers while we’re still designing. They often suggest tweaks we’d never have thought of — like choosing a different hinge, changing a snap-fit thickness, or tweaking a PCB shape to fit jigs.
🧪 Prototype to Learn, Not Just to Show
Every prototype we make teaches us something. Early-stage mockups help us catch assembly flaws, thermal issues, or part interferences well before tooling.
We don’t prototype for the sake of showing — we build to fail fast and learn faster.
🛠 Use DFM Tools, But Don’t Rely on Them Alone
We run mold flow simulations, FEA, and tolerance stacks — but we balance these with intuition from past builds. Not everything that works on-screen works on the bench.
🤝 Collaborate Closely With Suppliers
Our suppliers are partners. We regularly invite them into our design reviews, especially for complex parts — sheet metal bends, custom extrusions, or injection molded housings.
Their feedback often helps us reduce costs before locking tooling.
Real-World DFM in Action – BrahmWorks Case Studies
1. Smart Bed Frame – Integrated Fasteners
For our smart bed prototype, we swapped screw-based assembly with snap fits and captive inserts that reduced assembly time by 45%. The fasteners were integrated into the plastic mold design itself, saving cost and time.
2. Automotive Controller – PCB-First Housing
During enclosure design for a rugged motor controller, we reversed the process: designed the PCB first, then built the mechanical casing around its shape. This ensured optimal airflow and connector placement while eliminating unnecessary volume.
3. Sheet Metal Kiosk – Factory-Informed Assembly
In a digital signage kiosk project, our partner factory flagged a tricky weld joint during DFM review. Their suggestion? Convert the joint into a fold-and-tab lock using the existing tooling. Result: faster assembly, fewer steps, and stronger joints.
Streamline Your Product Journey with DFM at BrahmWorks
At BrahmWorks, designing for manufacturing is second nature. We don’t just deliver pretty renders — we build systems that are ready for the real world. That means fewer iterations, faster builds, and smoother handoffs to production.
Whether you’re building your first prototype or preparing for mass production, we can help you design smarter from the start.
Let’s build something that works — and works at scale.
FAQ: DFM with BrahmWorks
How early should I think about DFM?
Right from the start. The earlier we consider manufacturing, the fewer redesigns we’ll need later — which saves you time and money.
How long does the DFM process take?
It depends on complexity, but typically runs in parallel with design. We integrate DFM into every sprint — with checkpoints at concept, detail design, and pre-manufacturing.
What’s the difference between DFM and DFA?
DFM ensures parts are easy and cost-effective to manufacture. DFA ensures those parts are easy to assemble. At BrahmWorks, we do both — because one without the other doesn’t scale.